Case Study: Under Pressure
How Georgia-Pacific’s Quality Inspection Improved Box Integrity for a Plastics Compounder
Challenge
Plastics compounders serve a variety of industries, such as automotive parts and household appliances. One such company ships 750-kilogram pallets of its product from its plant in 48” x 45” x 39.5” octagonal boxes.
However, the company was facing serious quality control issues with its packaging. The glue joints on its boxes were popping frequently, causing structural failure. Many of the boxes wouldn’t make it from storage to transit, forcing employees to repack products in the warehouse, resulting in added expense and labor.
Solution
The plastics compounder called on Georgia-Pacific, who immediately invited the company to visit its Akron, Ohio, facility, which specializes in bulk packaging solutions. While there, the company saw first-hand the level of quality inspection missing from its previous supplier.
To remedy the structural issues of the containers, Georgia-Pacific experts made the following changes:
- Inspected one box out of every 20 produced for defects, including a full assessment of all glue joints.
- Performed compression and destructive tests on sample boxes, focusing on glue-joint failure and delamination concerns.
Based on its testing, Georgia-Pacific determined that insufficient operator attention to detail was the likely cause of the company’s troubles.
Result
The plastics company switched to Georgia-Pacific for its bulk containers and hasn’t looked back. The company’s shipping boxes are now strong enough to hold valuable cargo without collapsing. As a result, it no longer has the headache of repacking products, which saved time and improved efficiency. In addition, Georgia-Pacific’s responsive customer service ensures that boxes arrive within a day’s notice, reducing the need for forecasting and additional floor space for storage.
More Case Studies
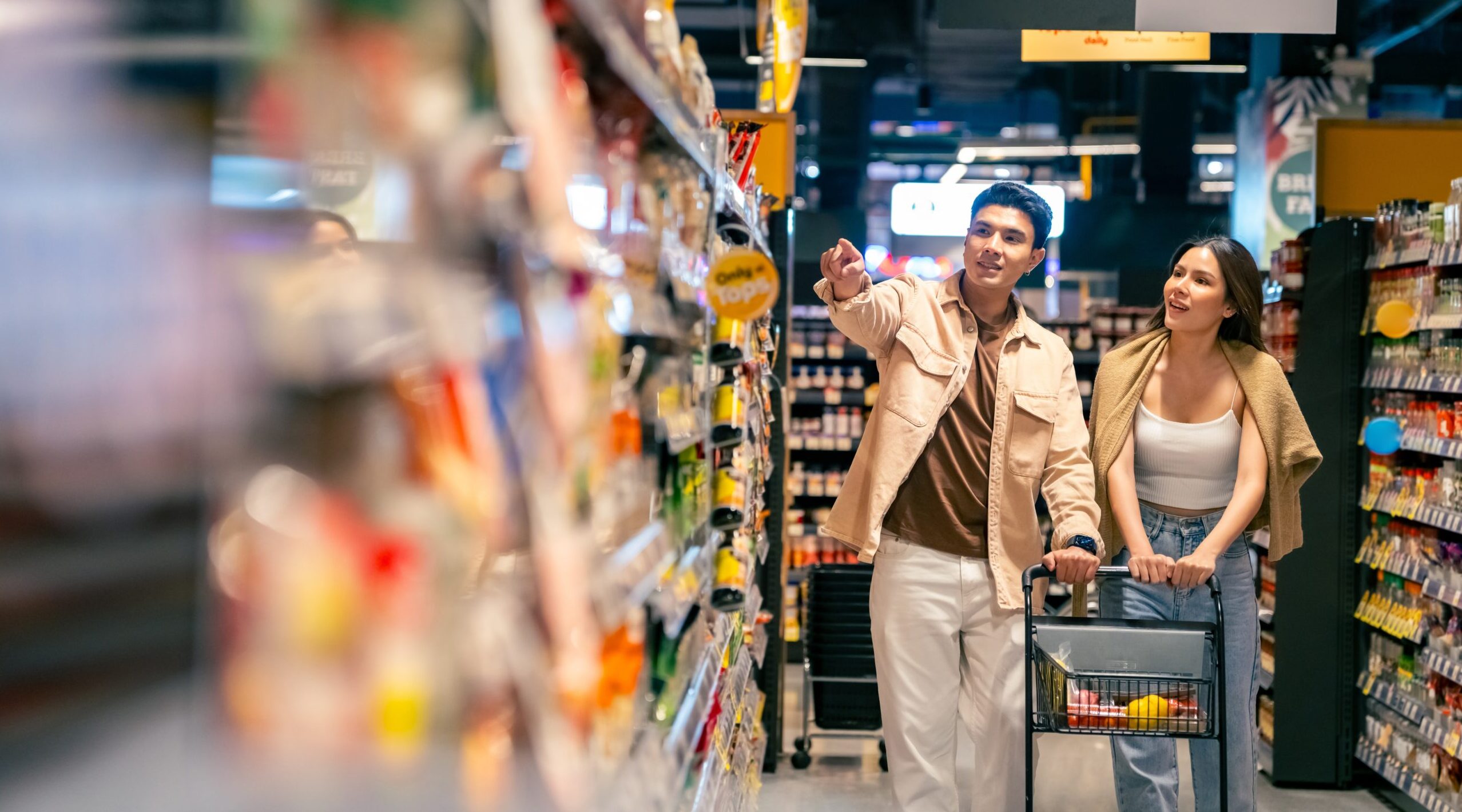
Snack Food Packaging
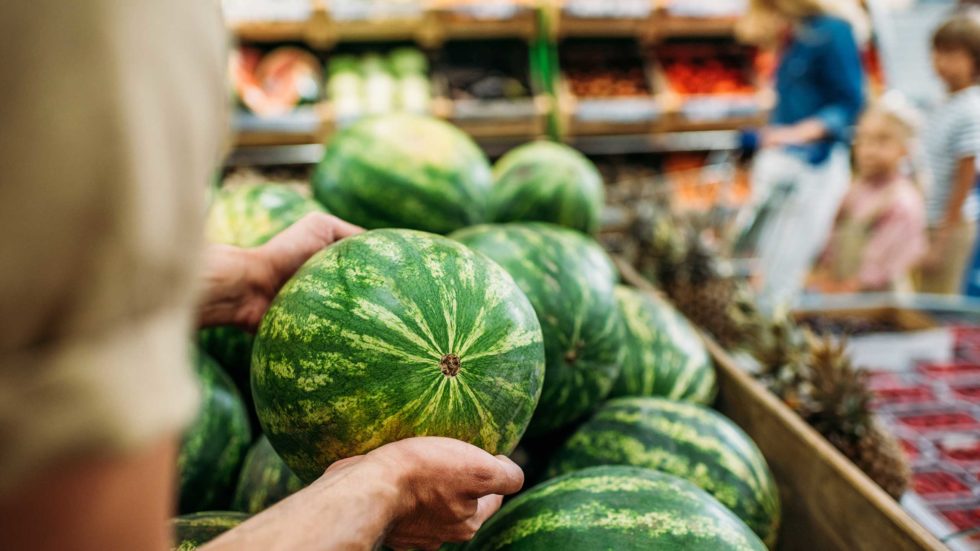
Savco speeds farm-to-store delivery with digitally printed corrugated bins
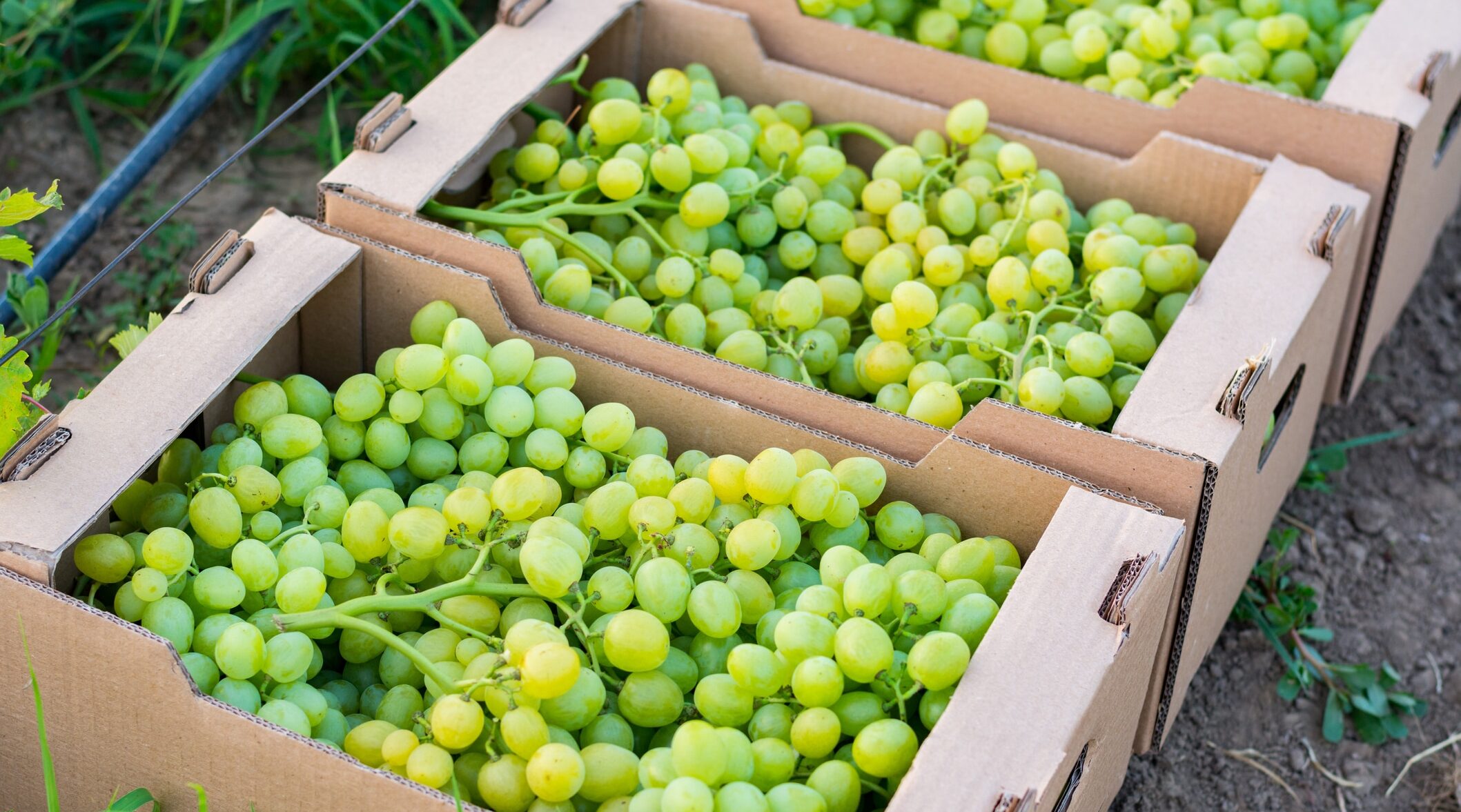